A prototype is generally defined as a preliminary version of a product, technology, or service that is intended to test and demonstrate its functionalities.
Prototyping allows the company to gather feedback from potential users and make necessary modifications to the design before launching the final product. It is an important step in the product development process, as it helps the company validate its ideas and make informed decisions about the direction of the project.
There are several different types of prototypes that can be used in the product development process. These types can be classified as:
- Concept prototypes: These are high-level prototypes that are used to test and evaluate the basics, or rather, the main concept or idea behind a proposed product or technology. They are typically very simple and may not include all of the features or functionality of the final product, however, these are not simply Proof of Concepts as they showcase how the final product will be featured.
- Design prototypes: These are appearances and may include some of the key features and functionality of the final product, but the final functionality is not the main objective. The objective is to showcase the fit of the functionalities in the proposed appearance.
- Functional prototypes: These are prototypes that are fully functional and include all the features and functionality of the final product. They are typically used to test and evaluate the usability and performance of the proposed product or technology.
- User experience prototypes: These are prototypes that are specifically designed to test and evaluate the user experience of a proposed product or technology. They may include elements of the product’s interface, such as buttons, menus, and navigation, but may not include all the functionality of the final product.
- Scale models: These are physical models of a proposed product that are used to test and evaluate the product’s size, shape, and proportions. They may be created using a variety of materials, including plastic, wood, or metal.
- Digital prototypes: These are prototypes that are created using computer-aided design (CAD) software. They are typically used to test and evaluate the design and functionality of a proposed product or technology in a virtual environment (e.g., Ansys).
Prototype is not a product; this has been already defined: however, let’s quickly brush over what else a prototype is or isn’t in the context of the product development cycle.
Prototype vs Proof of Concept (POC)
A For RVmagnetics, with the perspective of Research & Development activities to custom-create something that hasn’t been done yet – a Prototype and a Proof of Concept (POC) are two different stages in the product development cycle.
A prototype is a preliminary version of a product or technology that is used for static/dynamic testing and demonstration purposes, as mentioned above.
On the other hand, a proof of concept (POC) is a demonstration of the feasibility of a proposed concept or solution. It is typically a smaller-scale version of the final product and is used to test the basic functionality and underlying principlesof the proposed solution.
In other, simpler words – a POC shows if a feature will work, and a prototype shows how the final product will operate.
Both the prototype and POC are important steps in the product development cycle, as they help the company validate its ideas and make informed decisions about the direction of the project.
Successful and Unsuccessful Stories of Prototype
We believe it is important to learn from both successful and unsuccessful prototype launches alike. In fact, a failed prototype is surely better than a failed final product, so prototyping is first and foremost an exploratory investment activity to find the best possible option for taking an idea to market and to determine if it is overall relevant in the first place.
There are many success stories and failure examples of prototypes in the world of technology and product development. Likely one of the most known success stories is the development of the Apple iPhone. The original iPhone was a revolutionary device that combined a mobile phone, music player, and internet communicator into a single, easy-to-use device. Apple’s development team created multiple prototypes of the iPhone during the design and testing process and used feedback from users to make iterative improvements to the design. The final product was a huge success, and the iPhone has become one of the most popular and influential consumer electronics devices in history.
On the other hand, there are also many examples of failed prototypes in the tech industry. One notable example is Google Glass, a wearable computer with an optical head-mounted display. Google Glass was a highly anticipated product. Think about it: It seems like the ultimate device to have for a content creator and an everyday tech-savvy individual, right?
However, it failed to gain traction with consumers due to privacy concerns, technical limitations, and a high price tag. Despite the initial excitement and hype surrounding the product, Google Glass was ultimately discontinued in January 2015. Do you think the Facebook/Ray-Ban smart glasses (Ray-Ban Stories) will be any different?
In the context of failed prototypes, some companies may get “lucky” and not have to take the prototype to the customer testing stage before having to tank the whole project. Sure, it would have been nicer to recognize the issues and settle the project in POC stage, but it is also much better to have a failed prototype, that didn’t end up in public testing, eventually failing or even worse, succeeding and then failing in the mass manufactured form.
Tesla’s Solar Roof is a good example of this one: In 2016, Tesla unveiled a prototype for a solar roof that could generate electricity while also serving as the primary roofing material for a building. However, the company struggled with technical issues related to the durability and efficiency of the solar tiles, leading to delays and a slow roll-out of the product.
Project Loon is another example of a great idea, that failed to turn into MVP due to technical issues. This was a prototype for a network of high-altitude balloons that would provide internet access to remote areas was developed by Google X. One of the technical challenges faced by the project was the development of sensors and other technologies that could accurately measure and control the position and altitude of the balloons.
As a R&D service provider coming to market with the smallest passive sensors in the world, RVmagnetics aims to learn from examples of measurement/sensor prototypes as well. One of these good examples is the development of the Kinect sensor for the Xbox 360 video game console. The Kinect was a revolutionary device that used depth-sensing cameras and microphones to enable users to control and interact with the Xbox 360 using gestures and spoken commands. The development team at Microsoft created multiple prototypes of the Kinect during the design and testing process and used feedback from users to make iterative improvements to the design. The final product was a huge success, and the Kinect has been used in a variety of applications, including video gaming, home automation, and robotics.
Another successful example of a measurement/sensor prototype is the development of the LIDAR (Light Detection and Ranging) sensor for self-driving cars. LIDAR sensors use lasers to measure distances and create detailed 3D maps of the surrounding environment. This allows self-driving cars to accurately perceive and navigate their surroundings. The development of LIDAR sensors involved the creation of multiple prototypes, which were used to test and evaluate the feasibility, accuracy, and reliability of the technology. The final product has been widely adopted by self-driving car manufacturers and has been instrumental in advancing the development of autonomous vehicles.
These examples illustrate the importance of prototyping in the development of measurement and sensor technology. In the case of the Kinect and LIDAR sensors, prototyping played a crucial role in the development of these successful technologies.
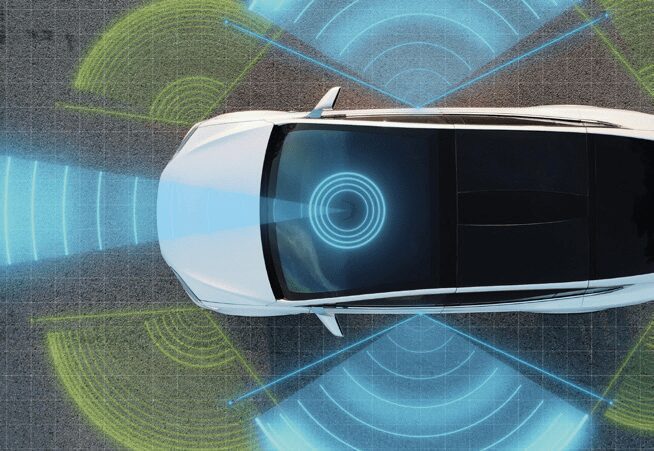
So, then what are the common reasons why a prototype ends up failing?
To name a few, especially relevant for prototypes with multiple stakeholders involved:
- Poor definition of objectives: If the objectives of the project are not clearly defined and understood by all stakeholders, it can lead to misunderstandings and misalignment throughout the project.
- Misalignment of expectations: It is important to align expectations with all stakeholders, including understanding the Technology Readiness Level (TRL) of the project. TRL is a common standard used to assess the maturity of a technology.
- Lack of resources: Also, a result of a false expectation setting, after certain POC, consultation and other evaluation efforts – prototyping projects will often require significant, even more resources, including personnel, funding, and equipment. If these resources are not available or are insufficient, it can lead to delays and setbacks – eventually a cancelled product, for the wrong reasons.
- Technical challenges: Prototyping projects often involve the development of new technologies or processes, which is as unpredictable as can be. If the project encounters technical issues that cannot be easily overcome, it can lead to de-funding, delays, and eventually unreleased products & technologies.
- Poor communication and collaboration: Effective communication and collaboration between team members and stakeholders are essential for the success of any project. If there are breakdowns in communication or a lack of collaboration, it can lead to misunderstandings and delays.
How Can a Prototype Lead to a Successful Product?
One of EU Tech Chamber advocates – RVmagnetics currently has key operations in the phase of developing new, and unique measurement systems based on their own, smallest passive sensor, MicroWire. Usually, they attend to use cases that other sensors were not able to address due to size, accuracy, wires and connections and other limitations (Microwires are thin and elastic like human hair and need no contact to provide accurate real time measurements).
This, for them, means custom-developing measurement solutions that haven’t been done before, thus acting as an outsourced research & development company for their partners: they develop POC, and prototypes of these new smartened products with new measurement features to ensure competitive growth.
- Clearly define the goals and objectives of the prototype: Before beginning the prototyping process, it is important to define the goals and objectives of the prototype clearly. This will help to ensure that the prototype is focused on addressing the key challenges and needs of the project and will provide a framework for evaluating the success of the prototype.
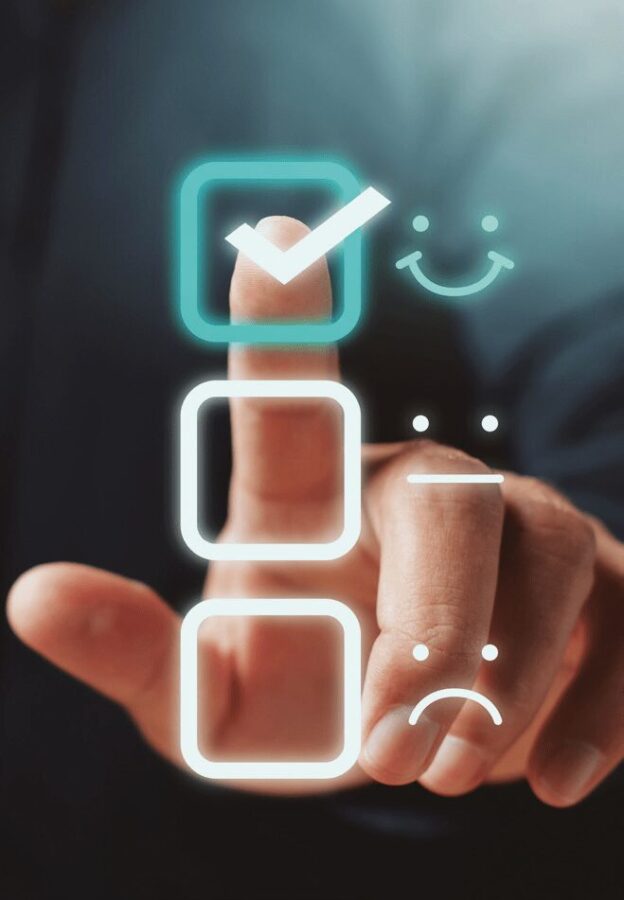
Clarify the value of the potential outcome that the product is aiming for.
- Involve potential users in the prototyping process: User feedback is critical to the success of a prototype. By involving potential users in the prototyping process, companies can gather valuable insights into how the proposed product or technology will be used and what features and functionality are most important to users.
- Test the prototype in a realistic environment: Prototyping should be conducted in a realistic environment that closely simulates the intended use of the product. This will allow the company to assess the feasibility, functionality, and effectiveness of the prototype under real-world conditions.
- Use interactive design techniques: By using interactive design techniques, companies can quickly identify and address most problems or challenges that arise and can improve the design of the prototype over time.
- Conduct thorough testing and evaluation: Before launching the final product, it is important to conduct thorough testing and evaluation of the prototype. This can be in the form of medium to long-term MVP use, adjustments in mass-manufacturing techniques, etc.
- Collect, consolidate, and archive the learnings: No matter the results, the prototype-creation process affects in learnings that will come in handy in future operations – both to use the gathered knowledge and experience in the relevant projects and to know better before stepping into an irrelevant one. If all the stakeholders archive their knowledge and experience properly, the accumulative work will be affective even if the responsible personnel within the companies are changing.
By following these steps, companies can increase the chances of success for their prototypes and ultimately for their new products. Prototyping is an essential part of the product development process and can help companies to validate their ideas, gather valuable feedback from users, and improve the chances of success for their products.

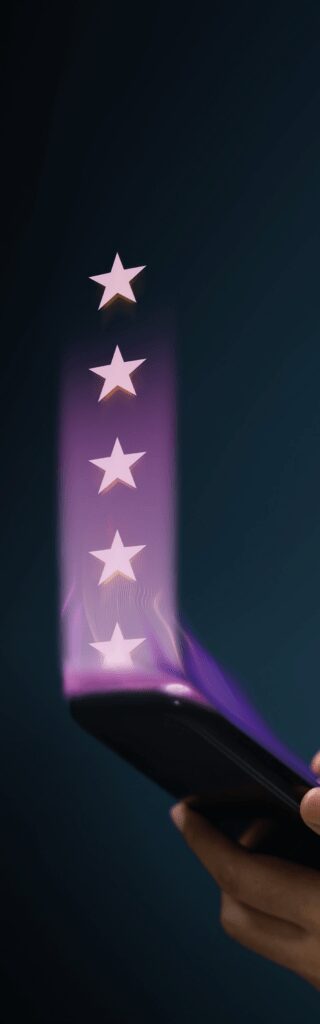